Warning
Important Notice: The DynaArm is currently a prototype and not ready for commercial use. It is intended solely for research and development purposes. Users are responsible for ensuring safe operation during its use.
System Overview
The DynaArm system is designed with a modular and scalable architecture, allowing seamless integration into diverse applications. This section provides a high-level overview of its hardware, electronics, and software.
Hardware
The DynaArm relies on lightweight yet robust components optimized for high precision and flexibility. Key features include:
Robotic Arm: Made from lightweight materials with 6 degrees of freedom (DoF) for precise motion.
Direct Drive Actuators: High-torque motors eliminate gearboxes, ensuring smooth operation and backdrivability.
ISO Standard End Effector: Compatible with ISO 9409-1-50-4-M6 flange for tool integration.
Key physical connections:
Power Supply: Requires an external 48 V power source.
Ethercat Interface: Primary communication protocol with the controller.
USB-C Interface: Provides auxiliary connectivity for peripherals like cameras.
Electronics
The system includes:
Motors: High-torque direct drive motors.
Sensors: Integrated encoders for position tracking and torque measurement.
Controller Unit: Manages real-time operation and communication with the Ethercat master.
Software
The DynaArm software is built on a modular ROS 2-based architecture, leveraging the following packages:
Package |
Description |
---|---|
Description package containing URDF and meshes for the DynaArm |
|
ros2_control based driver for the DynaArm. |
|
Demo applications for the DynaArm. Usually used for testing a new hardware setup. |
|
Underlying SDK for directly controlling the drives. Can be used to control the arm without ROS |
The software architecture is illustrated below:
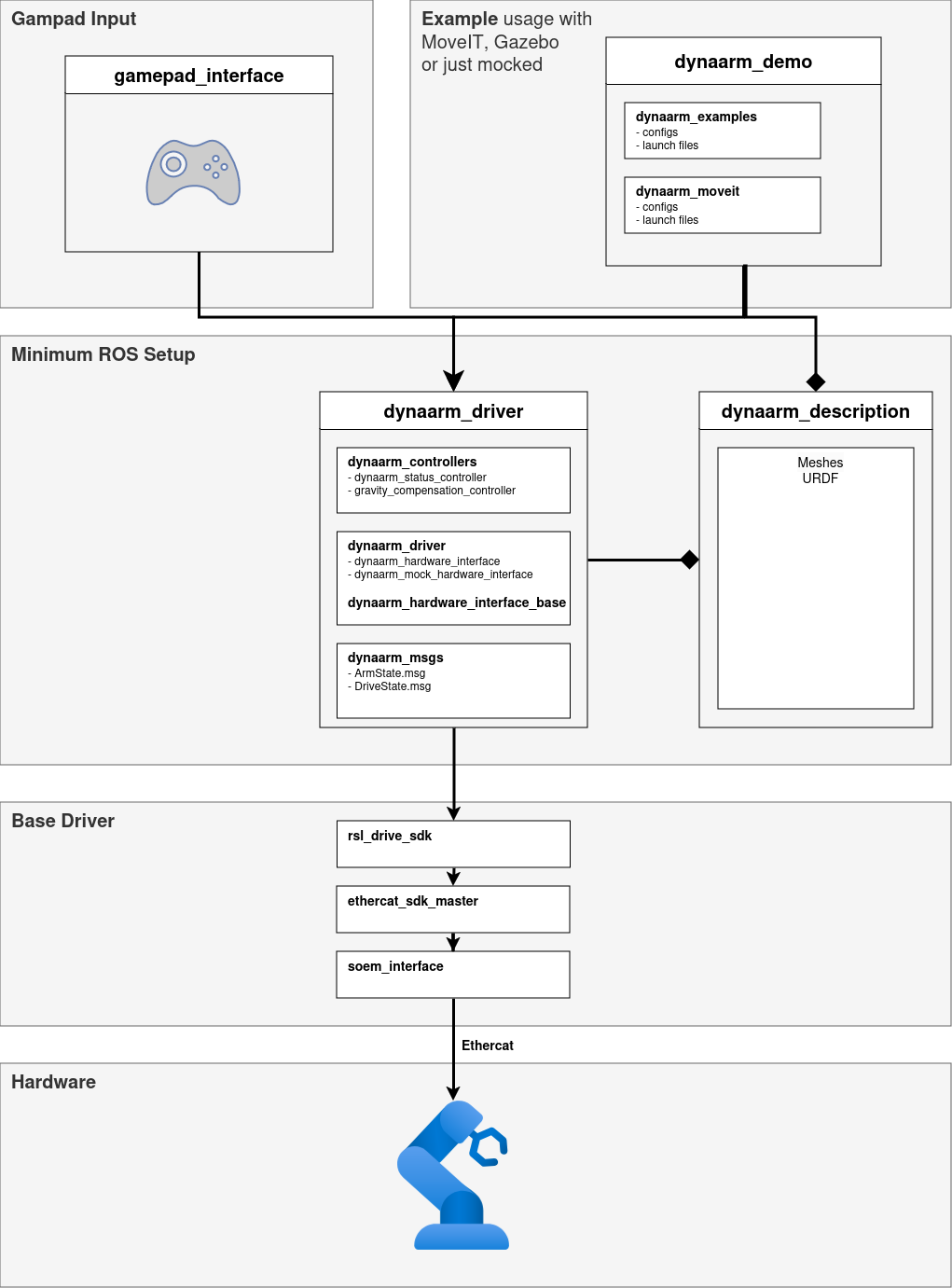
Risk Assessment
Important Note: As a prototype, the DynaArm has not undergone full risk evaluation. Users are advised to:
Operate on a stable surface and maintain a safe distance.
Regularly inspect connections and ensure reliability.
Use an emergency stop button for immediate shutdown in case of unexpected behavior.